Characteristics
The Obsidian model has been specially designed for multi-torch oxy-fuel cutting of structural steel, taking into account its specific properties. This makes Obsidian meet the demands of the heavy industry.
It is the ideal tool for those who require maximum performance and reliability, even under high thermal loads resulting from simultaneous cutting with multiple torches. Even in a demanding three-shift operation system, it delivers the highest efficiency and reliability.
Key Features
- Specialized Multi-Torch Oxygen Cutting:
Equipped for high-precision multi-torch operations, allowing simultaneous, accurate cuts. - Cutting Capacity:
Capable of cutting materials up to 300 mm thick. - Versatile Material Handling:
Efficiently cuts materials such as Hardox, structural steel, armor steel, and more. - Robust Construction:
Engineered with an integrated heavy-duty package to withstand the toughest industrial conditions. - Autonomous Oxygen Cutting:
Features advanced autonomous cutting capabilities, optimizing operations and eliminating the need for manual intervention. - Thermal Protection:
Equipped with thermal shields for the portal and sensitive components to ensure durability and reliability. - Comprehensive Safety Package:
Includes extensive safety measures to protect operators and equipment. - Industry 4.0 Compatibility:
Fully compatible with the Eckert Conneckt 4.0 system for seamless integration into modern, automated industrial environments. - Strip Cutting:
Adjustable nozzle spacing starting from 40 mm, enabling precise and customizable cutting processes.
Technology

System Multitorch
It enables simultaneous operation with multiple cutting torches, each functioning fully automatically. This system ensures high efficiency and repeatability of the cutting process, minimizes the risk of errors, and simplifies machine operation. The automation of each torch allows for efficient cutting without the need for a highly skilled operator, significantly increasing reliability and work efficiency.
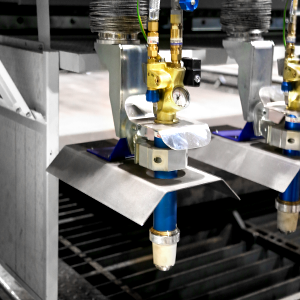
Autonomous Oxycut
The solution makes oxy-fuel cutting extremely simple, optimizing each stage of the process and significantly increasing cutting speed. The oxy-fuel torch, designed for cutting steel up to 300 mm thick, uses advanced sensors, including a height sensor, and an automatic ignition system, ensuring precision and minimizing operational errors. Thanks to the protective bellows and splash shields, the machine’s mechanisms and the operator are fully protected. The connection block for gas hoses simplifies servicing and eliminates downtime, ensuring efficient and uninterrupted production.
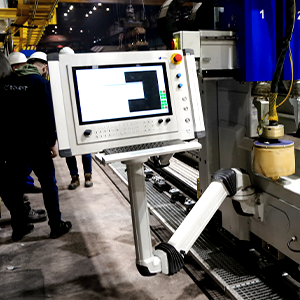
Eckert i-Vision controller
Modern industrial device equipped with a robust touchscreen made of Corning® Gorilla® Glass, designed for use in harsh environments. Thanks to its powerful components and proprietary software with extensive features and an intuitive user interface, it allows full utilization of the machine’s capabilities while ensuring reliable operation. The controller is mounted on an adjustable arm with a height range of +/- 300 mm, improving ergonomics for the operator and enabling comfortable control and monitoring of the cutting process. Furthermore, the Tropic/Frost system maintains the optimal temperature of the controller, increasing its durability and operational stability.There is also the possibility of integrating the controller with an additional computer that supports production planning systems like ERP and MES.
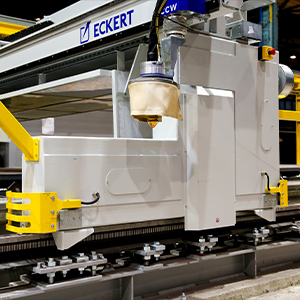
Construction
The portal, specially designed for the most challenging working conditions, made from welded steel profiles, offers exceptionally high rigidity while maintaining low weight. The heavy-duty package, along with robust drives and racks, further increases the machine’s reliability and durability. Thanks to this design, the machine maintains its high performance and precision even under extreme loads.

Heat shields
The additional heat shield effectively protects the machine from direct thermal radiation. The layers of ceramic fibers used for this purpose are located under the machine portal and carriages.
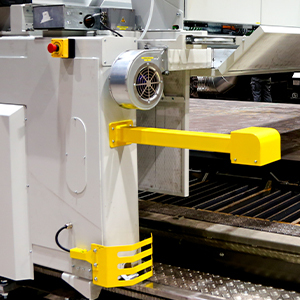
Temperature management system
The advanced active cooling system, using temperature sensors and fans, ensures a constant temperature inside and below the machine portal, even under extreme working conditions. This minimizes the risk of overheating electrical wiring and other electronic components, while ensuring consistent repeat accuracy.
Technical data
Model | Obsidian |
Drives | Serwo AC |
Cutting width | 2 000-12 000 mm |
Basic working length | From 1500 mm |
Positioning speed | 25000 mm/min |
Cutting thickness | up to 300 mm |
Cutting quality | DIN-EN ISO 9013 |
Positioning accuracy | DIN-EN 28206 |